“The society which scorns excellence in plumbing as a humble activity and tolerates shoddiness in philosophy because it is an exalted activity will have neither good plumbing nor good philosophy: neither its pipes nor its theories will hold water.”
John W. Gardner, Secretary,
Department of Health, Education, and Welfare, 1965
Introduction
Plumbing may be defined as the practice, materials, and fixtures used in installing, maintaining, and altering piping, fixtures, appliances, and appurtenances in connection with sanitary or storm drainage facilities, a venting system, and public or private water supply systems. Plumbing does not include drilling water wells; installing water softening equipment; or manufacturing or selling plumbing fixtures, appliances, equipment, or hardware. A plumbing system consists of three parts: an adequate potable water supply system; a safe, adequate drainage system; and ample fixtures and equipment.
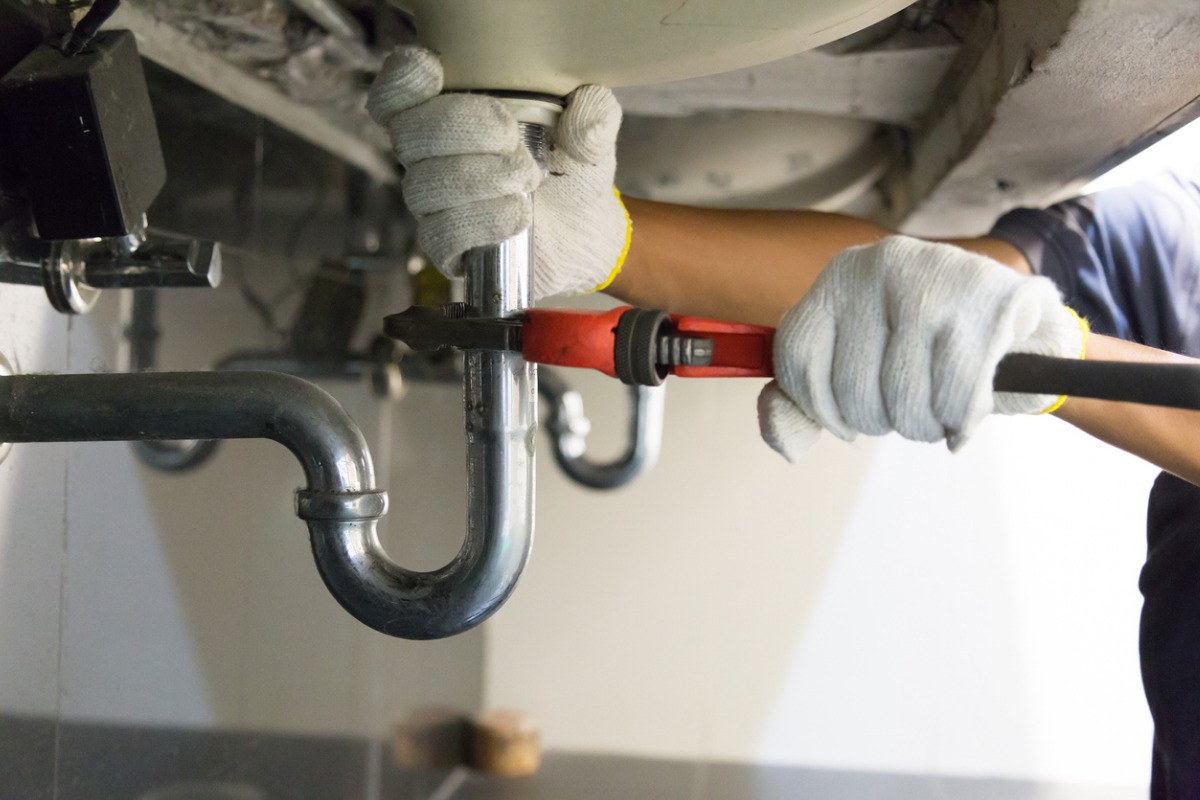
The housing inspector’s prime concern while inspecting plumbing is to ensure the provision of a safe water supply system, an adequate drainage system, and ample and proper fixtures and equipment that do not contaminate water. The inspector must make sure that the system moves waste safely from the home and protects the occupants from backup of waste and dangerous gases. This chapter covers the major features of a residential plumbing system and the basic plumbing terms and principles the inspector must know and understand to identify housing code violations that involve plumbing. It will also assist in identifying the more complicated defects that the inspector should refer to the appropriate agencies. This chapter is not a plumbing code, but should provide a base of knowledge sufficient to evaluate household systems.
Elements of a Plumbing System
The primary purposes of a plumbing system are
- To bring an adequate and potable supply of hot and cold water to the inhabitants of a house, and
- To drain all wastewater and sewage discharge from fixtures into the public sewer or a private disposal system.
It is, therefore, very important that the housing inspector be completely familiar with all elements of these systems so that inadequacies of the structure’s plumbing and other code violations will be recognized. To aid the inspector in understanding the plumbing system, a schematic of a home plumbing system is shown in Figure 9.1.
Water Service
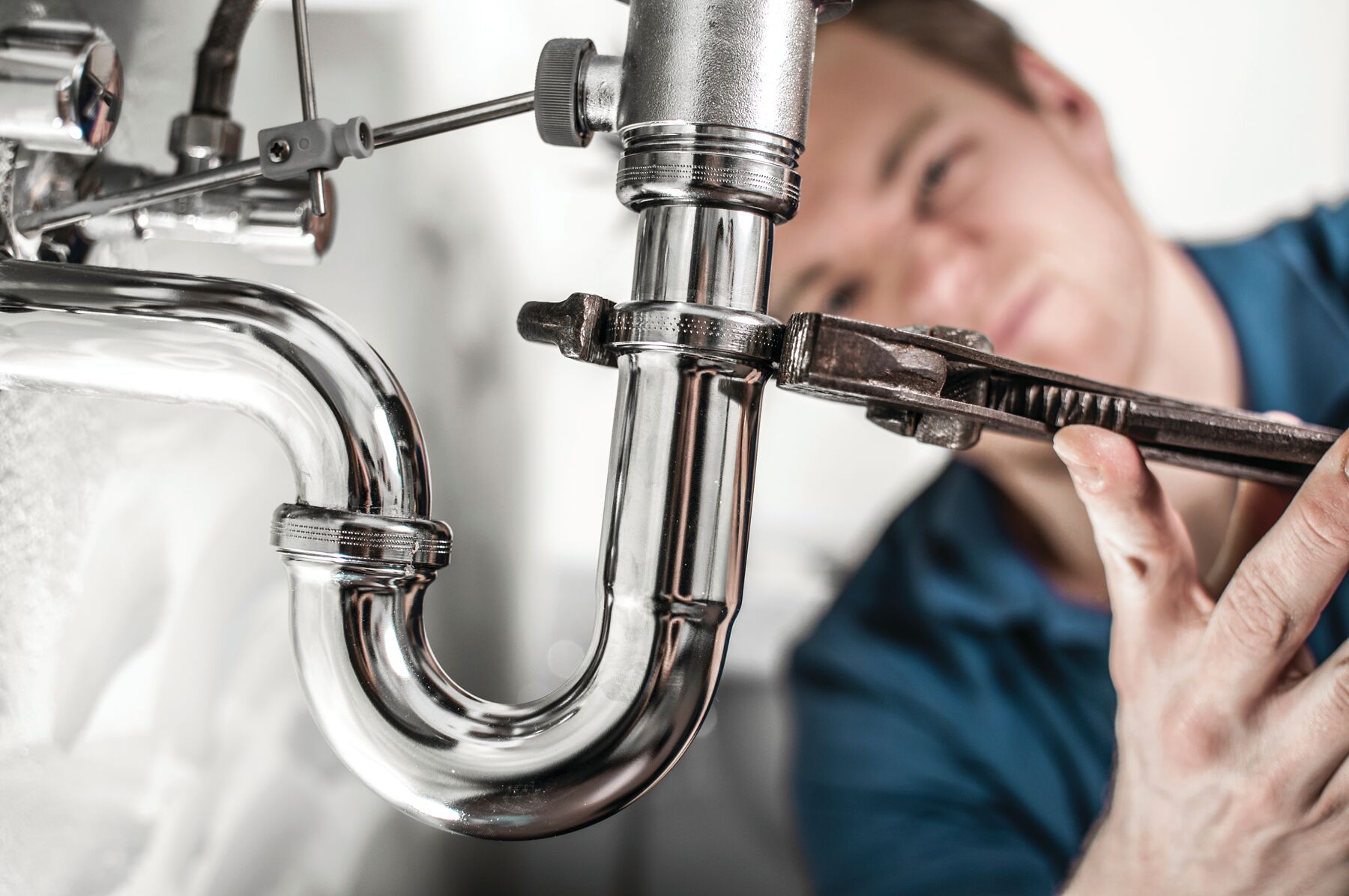
The piping of a house service line should be as short as possible. Elbows and bends should be kept to a minimum because they reduce water pressure and, therefore, the supply of water to fixtures in the house. The house service line also should be protected from freezing. Four feet of soil is a commonly accepted depth to bury the line to prevent freezing. This depth varies, however, across the country from north to south. The local or state plumbing code should be consulted for recommended depths. The minimum service line size should be ¾ inch. The minimum water supply pressure should be 40 pounds per square inch (psi), no cement or concrete joints should be allowed, no glue joints between different types of plastic should be allowed, and no female threaded PVC fittings should be used.
The materials used for a house service may be approved plastic, copper, cast iron, steel, or wrought iron. The connections used should be compatible with the type of pipe used. A typical house service installation is pictured in Figure 9.2. The elements of the service installation are described below.
Corporation stop—The corporation stop is connected to the water main. This connection is usually made of brass and can be connected to the main with a special tool without shutting off the municipal supply. The valve incorporated in the corporation stop permits the pressure to be maintained in the main while the service to the building is completed.
Curb stop—The curb stop is a similar valve used to isolate the building from the main for repairs, nonpayment, of water bills or flooded basements. Because the corporation stop is usually under the street and it is necessary to break the pavement to reach the valve, the curb stop is used as the isolation valve.
Curb stop box—The curb stop box is an access box to the curb stop for opening and closing the valve. A long-handled wrench is used to reach the valve.
Meter stop—The meter stop is a valve placed on the street side of the water meter to isolate it for installation or maintenance. Many codes require a gate valve on the house side of the meter to shut off water for plumbing repairs. The curb and meter stops can be ruined in a short time if used very frequently.
The water meter is a device used to measure the amount of water used in the house. It is usually the property of the water provider and is a very delicate instrument that should not be abused. In cold climates, the water meter is often inside the home to keep it from freezing. When the meter is located inside the home, the company providing the water must make appointments to read the meter, which often results in higher water costs unless the meter is equipped with a signal that can be observed from the outside. The water meter is not shown in Figure 9.2 because of regional differences in the location of the unit.
Because the electric system is sometimes grounded to an older home’s water line, a grounding loop device should be installed around the meter. Many meters come with a yoke that maintains electrical continuity even though the meter is removed.
Hot and Cold Water Main Lines
The hot and cold water main lines are usually hung from the basement ceiling or in the crawl space of the home and are attached to the water meter and hot water tank on one side and the fixture supply risers on the other. These pipes should be installed neatly and should be supported by pipe hangers or straps of sufficient strength and number to

prevent sagging. Older homes that have copper pipes with soldered pipes can pose a lead poisoning risk, particularly to children. In 1986, Congress banned lead solder containing greater than 0.2% lead and restricted the lead content of faucets, pipes, and other plumbing materials to no more than 8%. The water should be tested to determine the presence or level of lead in the water. Until such tests can be conducted, the water should be run for about 2 minutes in the morning to flush any such material from the line. Hot and cold water lines should be approximately 6 inches apart unless the hot water line is insulated. This is to ensure that the cold water line does not pick up heat from the hot water line [2].
The supply mains should have a drain valve stop and waste valve to remove water from the system for repairs. These valves should be on the low end of the line or the end of each fixture riser.
The fixture risers start at the basement main and rise vertically to the fixtures on the upper floors. In a one-family dwelling, riser branches will usually proceed from the main riser to each fixture grouping. In any event, the fixture risers should not depend on the branch risers for support, but should be supported with a pipe bracket.
The size of basement mains and risers depends on the number of fixtures supplied. However, a ¾-inch pipe is usually the minimum size used. This allows for deposits on the pipe due to hardness in the water and will usually give satisfactory volume and pressure.
In homes without basements, the water lines are preferably located in the crawl space or under the slab. The water lines are sometimes placed in the attic; however, because of freezing, condensation, or leaks, this placement can result in major water damage to the home. In two-story or multistory homes, the water line placement for the second floor is typically between the studs and, then, for the shortest distance to the fixture, between the joists of the upper floors.
Hot and Cold Water Piping Materials
Care must be taken when choosing the piping materials. Some state and local plumbing codes prohibit using some of the materials listed below in water distribution systems.
Polyvinyl Chloride (PVC). PVC is used to make plastic pipes. PVC piping has several applications in and around homes such as in underground sprinkler systems, piping for swimming pool pumping systems, and low-pressure drain systems PVC piping is also used for water service between the meter and building [3]. PVC, or polyvinyl chloride, is one of the most commonly used materials in the marketplace. It is in packaging, construction, and automotive material, toys, and medical equipment.
Chlorinated PVC. CPVC is a slightly yellow plastic pipe used inside homes. It has a long service life but is not quite as tough as copper. Some areas with corrosive water will benefit by using chlorinated PVC piping. CPVC piping is designed and recommended for use in hot and cold potable water distribution systems [4].
Copper. Copper comes in three grades:
- M for thin wall pipe (used mainly inside homes);
- L for thicker wall pipe (used mainly outside for water services); and
- K, the thickest (used mainly between water mains and the water meter).
Copper lasts a long time, is durable, and connects well to valves. It should not be installed if the water has a pH of 6.5 or less. Most public utilities supply water at a pH between 7.2 and 8.0. Many utilities that have source water with a pH below 6.5 treat the water to raise the pH. Private well water systems often have a pH below 6.5. When this is the case, installing a treatment system to make the water less acidic is a good idea [5].
Galvanized Steel. Galvanized pipe corrodes rather easily. The typical life of this piping is about 40 years. One of the primary problems with galvanized steel is that, in saturated water, the pipe will become severely restricted by corrosion that eventually fills the pipe completely. Another problem is that the mismatch of metals between the brass valves and the steel results in corrosion. Whenever steel pipe meets copper or brass, the steel pipe will rapidly corrode. Dielectric unions can be used between copper and steel pipes; however, these unions will close off flow in a short time. The problem with dielectric unions is that they break the grounding effect if a live electrical wire comes in contact with a pipe. Some cities require the two pipes to be bonded electrically to maintain the safety of grounded pipes.
PEX. PEX is an acronym for cross-formulated polyethylene. “PE” refers to the raw material used to make PEX (polyethylene), and “X” refers to the cross-linking of the polyethylene across its molecular chains. The molecular chains are linked into a three-dimensional network that makes PEX remarkably durable within a wide range of temperatures, pressures, and chemicals [6].
PEX is flexible and can be installed with fewer fittings than rigid plumbing systems. It is a good choice for repiping and for new homes and works well for corrosive water conditions. PEX stretches to accommodate the expansion of freezing water and then returns to its original size when the water thaws. Although it is highly freeze-resistant, no material is freeze-proof.
Kitec. Kitec is a multipurpose pressure pipe that uniquely unites the advantages of both metal and plastic. It is made of an aluminum tube laminated to interior and exterior layers of plastic. Kitec provides a composite piping system for a wide range of applications, often beyond the scope of metal or plastic alone. Unlike copper and steel materials, Kitec is noncorroding and resists most acids, salt solutions, alkalis, fats, and oils.
Poly. Poly pipe is a soft plastic pipe that comes in coils and is used for cold water. It can crack with age or wear through from rocks. Other weak points can be the stainless steel clamps or galvanized couplings.
Polybutylene [Discontinued]. Polybutylene pipe is a soft plastic pipe. This material is no longer recommended because of early chemical breakdown. Individuals with a house, mobile home, or other structure that has polybutylene piping with acetal plastic fittings may be eligible for financial relief if they have replaced that plumbing system.
Hot Water Safety
In the United States, more than 112,000 people enter a hospital emergency room each year with scald burns. Of these, 6,700 (6%), have to be hospitalized. Almost 3,000 of these scald burns come from tap water in the home. The three high risk groups are children under the age of 5 years, the handicapped, and adults over the age of 65 years. It only takes 1 second to get a serious third-degree burn from water that is 156ºF (69ºC). Tap water is too hot if instant coffee granules melt in it.
Young children, some handicapped individuals, and elderly people are particularly vulnerable to tap water burns. Children cannot always tell the hot water faucets from the cold water faucets. Children have delicate skin and often cannot get out of hot water quickly, so they suffer hot water burns most frequently. Elderly and handicapped persons are less agile and more prone to falls in the bath tub. They also may have diseases, such as diabetes, that make them unable to feel heat in some regions of the body, such as the hands and feet. Third-degree burns can occur quickly—in 1 second at 156ºF (69ºC), in 2 seconds at 149ºF (65ºC), in 5 seconds at 140ºF (60ºC), and in 15 seconds at 133ºF (56ºC).
A tap-water temperature of 120ºF–130ºF (49ºC–54ºC) is hot enough for washing clothes, bedding, and dishes. Even at 130ºF (54ºC), water takes only a few minutes of constant contact to produce a third-degree burn. Few people bathe at temperatures above 110ºF (43ºC), nor should they. Water heater thermostats should be set at about 120ºF (49ºC) for safety and to save 18% of the energy used at 140ºF (60ºC). Antiscald devices for faucets and showerheads to regulate water temperature can help prevent burns. A plumber should install and calibrate these devices. Most hot water tank installations now require an expansion tank to reduce pressure fluctuations and a heat trap to keep hot water from escaping up pipes.
Types of Water Flow Controls
It is essential that valves be used in a water system to allow the system to be controlled in a safe and efficient manner. The number, type, and size of valves required will depend on the size and complexity of the system. Most valves can be purchased in sizes and types to match the pipe sizes used in water system installations. Listed below are some of the more commonly encountered valves with a description of their basic functions.
Shutoff Valves. Shutoff valves should be installed between the pump and the pressure tank and between the pressure tank and service entry to a building. Globe, gate, and ball valves are common shutoff valves. Gate and ball valves cause less friction loss than do globe valves; ball valves last longer and leak less than do gate valves. Shutoff valves allow servicing of parts of the system without draining the entire system.
Flow-control Valves. Flow-control valves provide uniform flow at varying pressures. They are sometimes needed to regulate or limit the use of water because of limited water flow from low-yielding wells or an inadequate pumping system. They also may be needed with some treatment equipment. These valves are often used to limit flow to a fixture. Orifices, mechanical valves, or diaphragm valves are used to restrict the flow to any one service line or complete system and to assure a minimum flow rate to all outlets.
Relief Valves. Relief valves permit water or air to escape from the system to relieve excess pressure. They are spring-controlled and are usually adjustable to relieve varying pressures, generally above 60 psi. Relief valves should be installed in systems that may develop pressures exceeding the rated limits of the pressure tank or distribution system. Positive displacement and submersible pumps and water heaters can develop these excessive pressures. The relief valve should be installed between the pump and the first shutoff valve and must be capable of discharging the flow rate of the pump. Combined pressure and temperature relief valve are needed on all water heaters. Combination pressure and vacuum relief valves also should be installed to prevent vacuum damage to the system.
Pressure-reducing Valves. A pressure-reducing valve is used to reduce line pressure. On main lines, this allows the use of thinner walled pipe and protects house plumbing. Sometimes these valves are installed on individual services to protect plumbing.
Altitude Valves. Often an altitude valve is installed at the base of a hot water tank to prevent it from overflowing. Altitude valves sense the tank level through a pressure line to the tank. An adjustable spring allows setting the level so that the valve closes and prevents more inflow when the tank becomes full.
Foot Valves. A foot valve is a special type of check valve installed at the end of a suction pipe or below the jet in a well to prevent backflow and loss of prime. The valve should be of good quality and cause little friction loss.
Check Valves. Check valves have a function similar to foot valves. They permit water flow in only one direction through a pipe. A submersible pump may use several check valves. One is located at the top of the pump to prevent backflow from causing back spin of the impellers. Some systems use another check valve and a snifter valve. They will be in the drop pipe or pitless unit in the well casing and allow a weep hole located between the two valves to drain part of the pipe. When the pump is started, it will force the air from the drained part of the pipe into the pressure tank, thus recharging the pressure tank.
Frost-proof Faucets. Frost-proof faucets are installed outside a house with the shutoff valve extending into the heated house to prevent freezing. After each use, the water between the valve and outlet drains, provided the hose is disconnected, so water is not left to freeze.
Frost-proof Hydrants. Frost-proof hydrants make outdoor water service possible during cold weather without the danger of freezing. The shutoff valve is buried below the frost line. To avoid submerging it, which might result in contamination and back siphoning, the stop-and-waste valve must drain freely into a rock bed. These hydrants are sometimes prohibited by local or state health authorities.
Float Valves. Float valves respond to a high water level to close an inlet pipe, as in a tank-type toilet.
Miscellaneous Switches. Float switches respond to a high and/or low water level as with an intermediate storage tank. Pressure switches with a low-pressure cutoff stop the pump motor if the line pressure drops to the cutoff point. Low-flow cutoff switches are used with submersible pumps to stop the pump if the water discharge falls below a predetermined minimum operating pressure. High-pressure cut-off switches are used to stop pumps if the system pressure rises above a predetermined maximum. Paddle-type flow switches detect flow by means of a paddle placed in the pipe that operates a mechanical switch when flow in the pipe pushes the paddle.
The inadvertent contamination of a public water supply as a result of incorrectly installing plumbing fixtures is a potential public health problem in all communities. Continuous surveillance by environmental health personnel is necessary to know whether such public health hazards have developed as a result of additions or alterations to an approved system. All environmental health specialists should learn to recognize the three general types of defects found in potable water supply systems: backflow, back siphonage, and overhead leakage into open potable water containers. If identified, these conditions should be corrected immediately to prevent the spread of disease or poisoning from high concentrations of organic or inorganic chemicals in the water.
Water Heaters
Water heaters (Figure 9.3) are usually powered by electricity, fuel oil, gas, or, in rare cases, coal or wood. They consist of a space for heating the water and a storage tank for providing hot water over a limited period of time. All water heaters should be fitted with a temperature-pressure (T&P) relief valve no matter what fuel is used. The installation port for these valves may be found on the top or the side of the tank near the top. T&P valves should not be placed close to a wall or door jamb, where they would be inaccessible for inspection and use. Hot water tanks sometimes are sold without the T&P valve, and they must be purchased separately. This fact alone should encourage individual permitting and inspection by counties and municipalities to ensure that they are installed. The T&P valve should be inspected a minimum of once per year.
A properly installed T&P valve will operate when either the temperature or the pressure becomes too high due to an interruption of the water supply or a faulty thermostat. Figure 9.3 shows the correct installation of a gas water heater. Particular care should be paid to the exhaust port of the T&P valve. Figure 9.4 shows the placement of the T&P valve. This vent should be directed to within 6 inches of the floor, and care must be taken to avoid reducing the diameter of the vent and creating any unnecessary bends in the discharge pipe. Most codes will allow only one 90° bend in the vent. The point is to avoid any constrictions that could slow down the steam release from the tank to avoid explosive pressure buildup.
Water heaters that are installed on wooden floors should have water collection pans with a drainage tube that drains to a proper drain. The pan should be checked on a regular basis.
Tankless Water Heaters
A tankless unit has a heating device that is activated by the flow of water when a hot water valve is opened. Once activated, the heater delivers a constant supply of hot water. The output of the heater, however, limits the rate of the heated water flow. Demand water heaters are available in propane (LP), natural gas, or electric models. They come in a variety of sizes for different applications, such as a whole-house water heater, a hot water source for a remote bathroom or hot tub, or as a boiler to provide hot water for a home heating system. They can also be used as a booster for dishwashers, washing machines, and a solar or wood-fired domestic hot water system [7].
The appeal of demand water heaters is not only the elimination of the tank standby losses and the resulting lower operating costs, but also the fact that the heater delivers hot water continuously. Most tankless models have a life expectancy of more than 20 years. In contrast, storage tank water heaters last 10 to 15 years. Most tankless models have easily replaceable parts that can extend their life by many years more.
Drainage System
Water is brought into a house, used, and discharged through the drainage system. This system is a sanitary drainage system carrying just interior wastewater.
Sanitary Drainage System
The proper sizing of the sanitary drain or house drain depends on the number of fixtures it serves. The usual minimum size is 4 inches in diameter. The materials used are usually cast iron, vitrified clay, plastic, and, in rare cases, lead. The top two pipe choices for drain, waste, and vent (DWV) systems are PVC or ABS. For proper flow in the drain, the pipe should be sized and angled so that the pipe is approximately half full. This ensures proper scouring action so that the solids contained in the waste will not be deposited in the pipe.
Using PVC in DWV pipe is a two-step process needing a primer and then cement. ABS uses cement only. In most cases the decision will be made on the basis of which material is sold in an area. Few areas stock both materials because local contractors usually favor one or the other. ABS costs more than PVC in many areas, but Schedule 40 PVC DWV solid core pipe is stronger than ABS. Their durability is similar.
Size of House Drain. The Uniform Plumbing Code Committee has developed a method of sizing house drains in terms of fixture units. One fixture unit equals approximately 7½ gallons of water per minute. This is the surge flow rate of water discharged from a wash basin in one minute. All other fixtures have been related to this unit. Fixture unit values are shown in Table 9.1.
Table 9.1. Fixture Unit Values
Fixture | Units |
Lavatory/washbasin | 1 |
Kitchen sink | 2 |
Bathtub | 2 |
Laundry tub | 2 |
Combination fixture | 3 |
Urinal | 5 |
Shower bath | 2 |
Floor drain | 1 |
Slop sink | 3 |
Toilet | 1 or 3 (based on type) |
One bathroom group | 8 |
180 square feet of roof drain | 1 |
Grade of House Drain. A house drain should be sloped toward the sewer to ensure scouring of the drain. The usual pitch of a house or building sewer is a ¼-inch drop in 1 foot of length. The size of the drain is based on the fixture units flowing into the pipe and the slope of the drain.
Table 9.2 shows the required pipe size for the system.
Table 9.2. Sanitary House Drain Sizes
Diameter of Pipe, Inches | Maximum Number of Fixtures per Listed Drain Slope† | ||
1/8 inch per foot | ¼ inch per foot | ½ inch per foot | |
1¼ | 1 | 1 | 1 |
1½ | 2 | 2 | 3 |
2 | 5 | 6 | 8 |
3 | 15 | 18 | 21 |
4 | 84 | 96 | 114 |
6 | 300 | 450 | 600 |
8 | 990 | 1,392 | 2,220 |
12 | 3,084 | 4,320 | 6,912 |
†Number of fixture units. |
House Drain Installation. Typical branch connections to the main are shown in Figure 9.5.
Fixture and Branch Drains. A branch drain is a waste pipe that collects the waste from two or more fixtures and conveys it to the sewer. It is sized in the same way as the sewer, taking into account that all toilets must have a minimum 3-inch diameter drain, and only two toilets may connect into one 3-inch drain. All branch drains must join the house drain with a Y-fitting as shown in Figure 9.5. The same is true for fixture drains joining branch drains. The Y-fitting is used to eliminate, as much as possible, the deposit of solids in or near the connection. A buildup of these solids will block the drain. Recommended minimum sizes of fixture drains are shown in Table 9.2 .
Traps
A plumbing trap is a device used in a waste system to prevent the passage of sewer gas into the structure and yet not hinder the fixture’s discharge to any great extent. All fixtures connected to a household plumbing system should have a trap installed in the line. The effects of sewer gases on the human body are well known; many of the gases are extremely harmful. In addition, certain sewer gases are explosive.
P-trap. The most commonly used trap is the P-trap (Figure 9.6). The depth of the seal in a trap is usually 2 inches. A deep seal trap has a 4-inch seal.
As mentioned earlier, the purpose of a trap is to seal out sewer gases from the structure. Because a plumbing system is subject to wide variations in flow, and this flow originates in many different sections of the system, pressures vary widely in the waste lines. These pressure differences tend to remove the water seal in the trap. The waste system must be properly vented to prevent the traps from siphoning dry, thus losing their water seal and allowing gas from the sewer into the building.
Objectionable Traps. The S-trap and the ¾ S-trap (Figure 9.7) should not be used in plumbing installations. They are almost impossible to ventilate properly, and the ¾ S-trap forms a perfect siphon. Mechanical traps were introduced to counteract this problem. It has been found, however, that the corrosive liquids flowing in the system corrode or jam these mechanical traps. For this reason, most plumbing codes prohibit mechanical traps.
The bag trap, an extreme form of S-trap, is seldom found. Figure 9.7 also shows this type of S-trap.
Traps are used only to prevent the escape of sewer gas into the structure. They do not compensate for pressure variations. Only proper venting will eliminate pressure problems.
Ventilation
A plumbing system is ventilated to prevent trap seal loss, material deterioration, and flow retardation.
Trap Seal Loss. The seal in a plumbing trap may be lost due to siphonage (direct and indirect or momentum), back pressure, evapo ration, capillary attraction, or wind effect. The first two are probably the most common causes of loss. Figure 9.8 depicts this siphonage process; Figure 9.9 depicts loss of trap seal.
If a waste pipe is placed vertically after the fixture trap, as in an S-trap, the wastewater continues to flow after the fixture is emptied and clears the trap. This is caused by the pressure of air on the water of the fixture being greater than the pressure of air in the waste pipe. The action of the water discharging into the waste pipe removes the air from that pipe and thereby causes a negative pressure in the waste line.
In the case of indirect or momentum siphonage, the flow of water past the entrance to a fixture drain in the waste pipe removes air from the fixture drain. This reduces the air pressure in the fixture drain, and the entire assembly acts as an aspirator. (Figures 9.10 and 9.11 show plumbing configurations that would allow this type of siphonage to occur.)
Back Pressure. The flow of water in a soil pipe varies according to the fixtures being used. Small flows tend to cling to the sides of the pipe, but large ones form a slug of waste as they drop. As this slug of water falls down the pipe, the air in front of it becomes pressurized. As the pressure builds, it seeks an escape point. This point is either a vent or a fixture outlet. If the vent is plugged or there is no vent, the only escape for this air is the fixture outlet.
The air pressure forces the trap seal up the pipe into the fixture. If the pressure is great enough, the seal is blown out of the fixture entirely. Figures 9.8 and 9.9 illustrate the potential for this type of problem. Large water flow past the vent can aspirate the water from the trap, while water flow approaching the trap can blow the water out of the trap.
Vent Sizing. Vent pipe installation is similar to that of soil and waste pipe. The same fixture unit criteria are used. Table 9.3 shows minimum vent pipe sizes.
Table 9.3. Minimum Fixture Service Pipe Diameters [8]
Fixture | Supply Line, Inches | Vent Line, Inches | Drain Line, Inches |
Bathtub | ½ | 1½ | 1½ |
Kitchen Sink | ½ | 1½ | 1½ |
Lavatory | 3/8 | 1¼ | 1¼ |
Laundry Sink | ½ | 1½ | 1½ |
Shower | ½ | 2 | 2 |
Toilet Tank | 3/8 | 3 | 3 |
*Millimeters in parenthesis. |
Vent pipes of less than 1¼ inches in diameter should not be used. Vents smaller than this diameter tend to clog and do not perform their function.
Individual Fixture Ventilation. Figure 9.12 shows a typical installation of a wall-hung plumbing unit. This type of ventilation is generally used for sinks, drinking fountains, and so forth. Air admittance valves are often used for individual fixtures. Figure 9.13 shows a typical installation of a bathtub or shower ventilation system. Figure 9.14 shows the proper vent connection for toilet fixtures and Figure 9.15 shows a janitor’s sink or slop sink that has the proper P-trap. For the plumbing fixture to work properly, it must be vented as in Figures 9.13 and 9.14.
Unit Venting. Figures 9.10 and 9.11 show a back-to-back shared ventilation system for various plumbing fixtures. The unit venting system is commonly used in apartment buildings. This type of system saves a great deal of money and space when fixtures are placed back-to-back in separate apartments. It does, however, pose a problem if the vents are undersized because they will aspirate the water from the other trap. Figure 9.16 shows a double combination Y-trap used for joining the fixtures to the common soil pipe fixture on the other side of the wall.
Wet Venting. Bathroom fixture groupings are commonly wet vented; that is, the vent pipe also is used as a waste line.
Total Drainage System
The drain, soil waste, and vent systems are all connected, and the inspector should remember the following fundamentals:
Working vents must provide air to all fixtures to ensure the movement of waste into the sewer. Improperly vented fixtures will drain slowly and clog often. They also present a health risk if highly toxic and explosive sewer gases enter the home. Correct venting is shown in Figures 9.10, 9.11, 9.12, 9.13, 9.14, and 9.15; incorrect venting is shown in Figures 9.8 and 9.9. A wet vent can result in one of the traps siphoning the other dry when large volumes of water are poured down the drain. Wet vents are not permitted by many state plumbing codes because of the potential for self-siphoning.
Backup of sewage into sinks, dishwashers, and other appliances is always a possibility unless the system is equipped with air gaps or vacuum breakers. All connections to the potable water system must be a minimum of two pipe diameters above the overflow of the appliance and, in some cases, where flat surfaces are near, two and one-half pipe diameters above the overflow of the appliance.
A simple demonstration of how easily siphoning can occur is to hold a glass of water with food coloring in it with the tip of a faucet in the colored water. If the sink’s vegetable sprayer is directed to a second glass and sprayed, in most cases, the colored water will be aspirated into the faucet and then out of the sprayer into the second glass. Weed or pest killer attachments that hook to garden hoses work on the same principle. Figure 9.17 shows an outside hose bib equipped with a vacuum breaker. In the areas of the United States that freeze, these vacuum breakers must be removed because they trap water in the area of the line that can freeze and burst. Many vacuum breakers sold today automatically drain to prevent freeze damage.
Devices that pull water from a utility may create negative pressures that can damage water piping and pull dangerous sub-stances into the line at the same time. These devices include power sprayers that hook to the home hose bib (outside faucets) and pressurize the spray by creating a vacuum on the supply side.
Corrosion Control
To understand the proper maintenance procedures for the prevention and elimination of water quality problems in plumbing systems, it is necessary to understand the process used to determine the chemical aggressiveness of water. The process is used to determine when additional treatment is needed. Water that is out of balance can result in many negative outcomes, from toxic water to damaged and ruined equipment.
Water dissolves and carries materials when it is not saturated. An equilibrium among pH, temperature, alkalinity, and hardness controls water’s ability to create scale or to dissolve the material. If water is saturated with harmless or beneficial substances, such as calcium, then the threat of damage can be mitigated. The Langelier method, developed in the early 1930s, is a process used in boiler management, municipal water treatment, and swimming pools to provide this balance. In the Langelier index, saturation over 0.3 is scale forming, and a saturation below 0.3 is corrosive.
The susceptibility of metal to corrosion is as follows (most susceptible to least susceptible): magnesium, zinc, aluminum, cadmium, mild steel, cast iron, stainless steel (active), lead-tin solder, lead, tin, brass, gunmetal, aluminum bronze, copper, copper-nickel alloy, Monel, titanium, stainless steel (passive), silver, gold, and platinum.
Water Conservation
How much attention should be paid to fixtures that just drip a little bit of water or that just will not quite shut off? At 30 drops per minute, you will lose and pay for 54 gallons per month. At 60 drops per minute, you will lose and pay for 113 gallons per month. At 120 drops per minute, you will lose and pay for 237 gallons per month.
This is only a small loss of water considering the 5 to 7 gallons per flush used by a properly functioning toilet. If the toilet is not properly maintained, the loss of water and its effect on the monthly water bill can be incredible. Lower flow toilets have been mandated to save precious and limited resources. Most pre-1992 toilets used up to 7 gallons per flush. Toilets have since evolved to use 5.5, then 3.5, and now 1.6 gallons per flush.
With the changes in the water usage laws in 1992, there were many customer complaints, and plumbers were in the bad position of installing products that nobody wanted to use. New and updated products now work better than the old water wasters.
According to the EPA, in 2000, a typical U.S. family of four spent approximately $820 every year on water and sewer fees, plus another $230 in energy for heating water. In many cities, according to the U.S. EPA, water and sewer costs can be more than twice those amounts. Many people do not realize how much money they can save by taking simple steps to save water, and they do not know the cumulative effects small changes can have on water resources and environmental quality. Fixing a leaky faucet, toilet, or lawn-watering system can reduce water consumption. Changing to water-efficient plumbing fixtures and appliances can result in major water and energy savings [9,10].
Summer droughts remind many of the need to appreciate clean water as an invaluable resource. As the U.S. population increases, the need for clean water supplies continues to grow dramatically and puts additional stress on our limited water resources. We can all take steps to save and conserve this valuable resource.
The EPA [11] suggests the following steps homeowners should take right away to save water and money:
- Stop leaks!—Check indoor water-using appliances and devices for leaks. Pay particular attention to toilets that leak.
- Take showers—Showers use considerably less water than do baths.
- Replace showerheads—Replacement shower heads are available that reduce water use.
- Turn the water off when not needed—While brushing your teeth, turn the water off until you need to rinse.
- Replace your old toilet—The largest water user inside the home is the toilet. If a home was built before 1992 and the toilet has never been replaced, likely, it is not a water-efficient, 1.6 gallons-per-flush toilet. Choose a replacement toilet carefully to ensure that what you make an upper individual flush, you do not lose because you must flush more often.
- Replace your clothes washer—The second largest water user in the home is the washing machine. Energy Star-rated washers that also have a water factor at or lower than 9.5 use 35%–50% less water and 50% less energy per load. This saves money on both water and energy bills.
- Plant the right plants with proper landscape design and irrigation—Select plants that are appropriate for the local climate. Having a 100% turf lawn in a desert climate uses a significant amount of water. Also, homeowners should consider the benefits of a more natural landscape.
- Water plants only as needed—Most water wasted in the garden is by watering when plants do not need it or by not maintaining the irrigation system. If manually watering, set a timer and move the hose promptly. Make sure the irrigation controller has a rain shutoff device and that it is appropriately scheduled. Drip irrigation should be considered where practical. Newer irrigation systems have sensors to prevent watering while it is raining
Putting It All Together
The photographs below, taken during construction of a home by Habitat for Humanity, show various plumbing elements discussed in this chapter.
Roughed-in clothes washer.
Hot and cold copper water lines and drain, P-trap and vent, and vent for the washer drain. When a house is vacant for a while, the P-trap should be filled with water to prevent sewer gas from entering the home. Mineral oil added to the water can slow the loss of fluid in the trap.
Roughed-in sink.
Hot and cold water pipes, soil pipe, and vent showed.
Roughed-in bathroom.
Vent for the sink and toilet, soil pipe, and cap for toilet connection shown. A wax or plastic seal shaped like a donut will be placed on the cap before bolting down the toilet.
Back of a fiberglass shower/bathtub combination.
Mixing and anti-scald water flow control, vent for the fixture, hot and cold water lines, and bathtub overflow is shown. At this point in construction, insulation might be considered for the hot water lines.
Water service and wastewater line.
Polyethylene water service pipe enters the home through the concrete basement wall shown. The white plastic adapter is shown between the polyethylene water service pipe and ¾ inch copper water line. A short distance above the adapter is a pressure-reducing valve. To the right of the water, the line is the 4 inch PVC pipe wastewater line.